Setting Standards in Delivering EPC Projects
We provide a wide range of professional services to meet your needs. We promise to provide every service with a smile, and to your highest level of satisfaction.
Robust Project Methodology
Lucky Group over years has developed proven project execution methodology. Systematic phases of project execution includes :
➧ Design & Engineering
- Concept Design
- Feasibility Studies
- Basic Engineering
- Detailed Engineering
➧ Procurement
➧ Planning & Reporting
➧ Mobilization & Site Survey
➧ Material Handling
➧ Construction & Construction Management
➧ Safety Management
➧ Quality Management
➧ Mechanical Completion
➧ Pre-commissioning
➧ Commissioning, Functional Tests & Start-up
➧ Plant Handover
➧ Operations & Maintenance Training
➧ Final Documentation
➧ Project Closeout
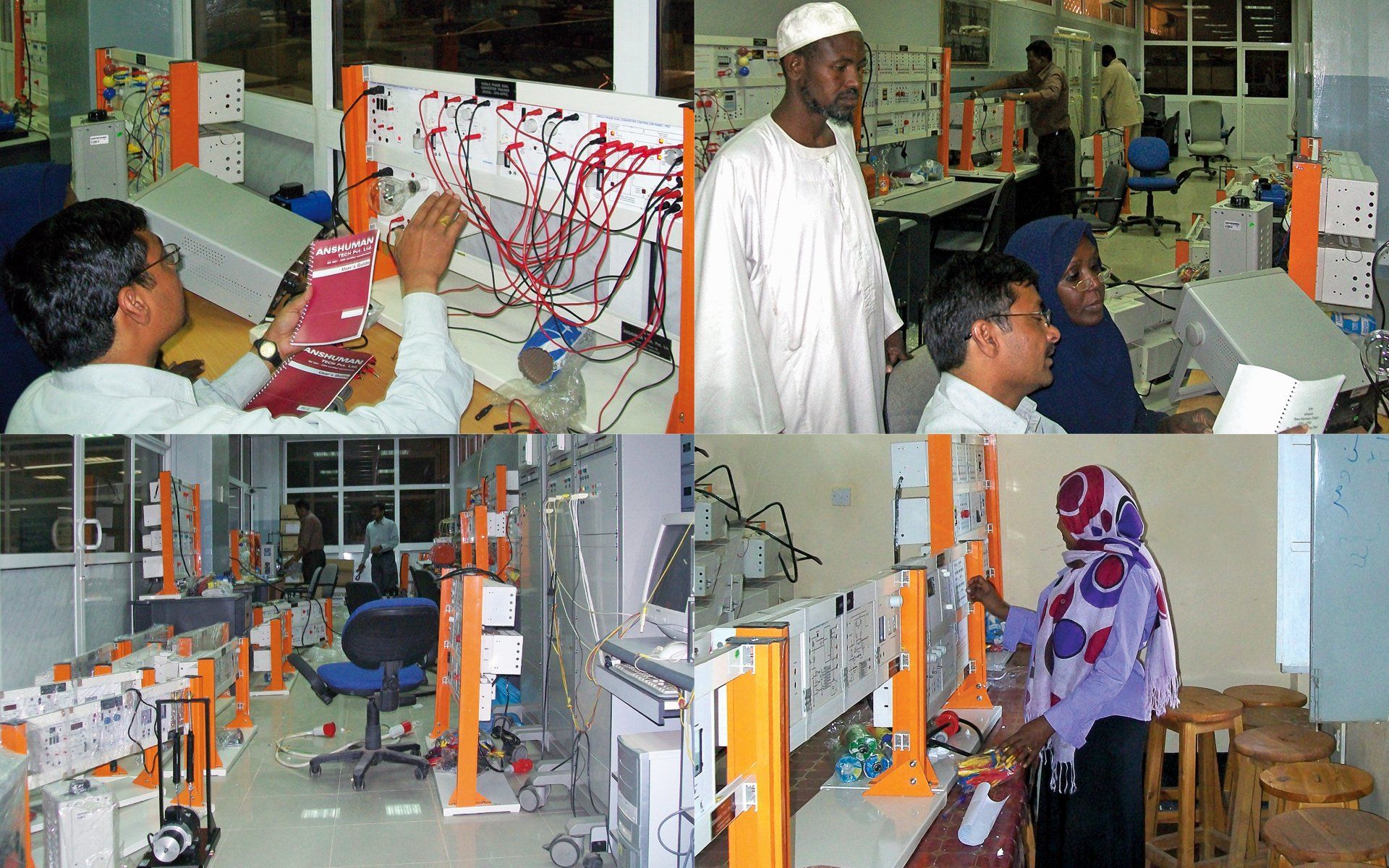
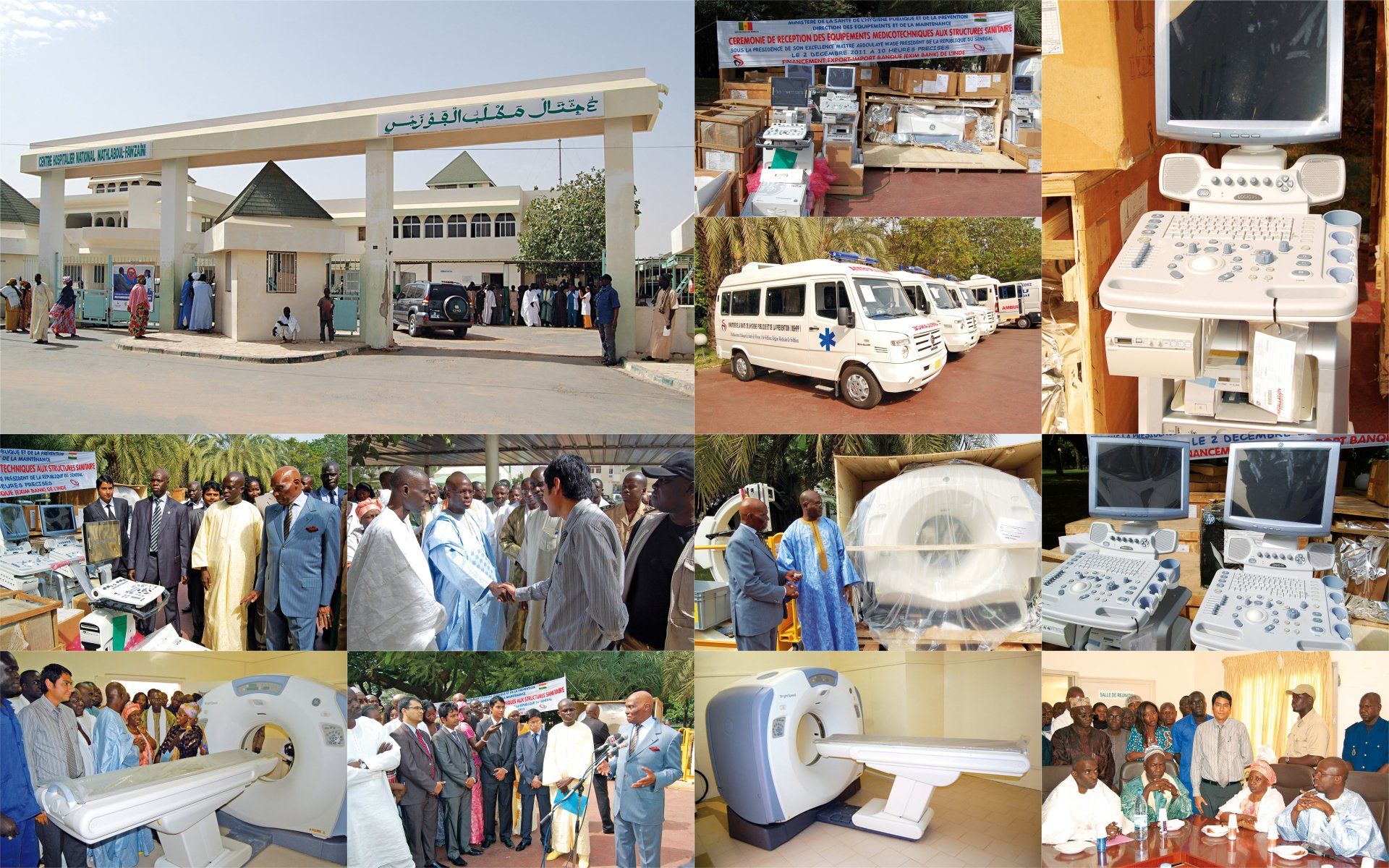
Design & Engineering
• Concept Design
• Feasibility Studies
• Basic Engineering
• Detailed Engineering
Procurement
Process of acquiring goods or services from an external source usually by means of competitive bidding
Conduct Procurement : Deciding on Prospective Vendors/Manufacturers
Control Procurement : Ensuring that product/service being provided is as per requirements
Close Procurement : Confirming that all obligations are fulfilled at both ends
Planning & Reporting
Project planning is part of project management, which relates to the use of schedules such as Gantt charts to plan and subsequently report progress within the project environment.This Phase defines the “What, When, How & Who” for the Project. This process comprises of :
• Rolling Wave Planning : Progressive Elaboration of Scope is carried out
• Development of Baselines : Scope, Schedule and Cost Baselines are prepared
• Manpower Planning : Forming a Project Team with the skill set suiting the project
Mobilization & Site Survey
Activation of physical and manpower resources for transfer to a construction site until the completion of the contract. A careful survey plan will help clients focus on the project, while guiding their implementation and analysis so the survey research is finished quicker. Every survey plan should include consideration of the following six areas :
• Survey Value
• Survey Cost
• Defining the Project
• Defining the Audience
• Defining the Project Team
• Defining the Audience
Material Handling
Planning the transportation of resources (Equipment, Spares and consumables) to a central location and managing its warehousing, distribution and consumption thereafter.
Construction & Construction Management
Planning & Organizing the mobilization equipment, material, and personnel for performing construction activities
The underlying objectives are as follows :
- Delivering desired results within the agreed timeframe
- Maximizing the resource efficiency and in turn maintain the efficiency of Operations through proper coordination and control
- Minimizing the possibility of Conflicts by practising effective communication & efficient processes.
Safety Management
Formulation of policy, plans and procedures to manage safety elements such that potential risks are reduced to levels that are acceptable
The basic components are :
- Risk Readiness - How is the organization ready to manage risks ?
- Identifying Risk -Assessing the potential risks at workplace/site
- Risk Response -Implementing Risk Control/Response
- Communication -Communicating effectively across the organization
- Regular Audits -Identifying non conformities in the system and correcting them.
- Updated Systems -Implementing continuous improvement
Quality Management
Lucky Group's Quality Assurance process, plans and procedures ensure that all deliverables are either meeting or exceeding customer expectations.
The main components of Lucky Group's Quality management are
- Quality Planning
- Quality Assurance
- Quality Control
- Quality Improvement
Mechanical Completion
The final phases of the construction work under the provisions of the Prime Contract and in accordance with the testing, turnover and acceptance information in the Project.
Includes Erection and Assembly of facilities including installation of Equipment, Sub-assemblies and Parts. Performance of non-operating adjustments, leaks, pressure testing, other non-destructive tests and cold alignment checks.
Pre-commissioning
Pre-commissioning includes Instrument calibration and loop checks, electrical continuity and motor rotation checks made by contractor or subcontractors prior to mechanical completion. Instrument calibration and loop checks, electrical continuity and motor rotation checks are completed and the facilities are ready for commissioning.
Commissioning, Functional Tests & Start-up
The commissioning phase of the work generally commences shortly before Mechanical Completion and terminates prior to the introduction of feed. Commissioning activities required to ready the plant for startup are as follows :
- Purging
- Flushing and cleaning
- Commissioning and testing of utilities
- Instrument loop calibration
- Function Loop checks
- Control System Checkout
- Emergency shutdown / safety system checkout
- Refractory dry-out
- Rotating equipment run-in
- Tightness testing
- Chemical and catalyst loading
- Insulation Resistance / Megger Test
- Earth Resistance Tests
Plant Handover
Plant / Project handover procedures are exhaustive, which include :
- Operational Knowledge Transfer
- Critical Equipment list
- Safe Work Instructions
- Troubleshooting Guides
- Isolation Proceedures
- Maintenance Strategy
- Maintenance Manuals
- Equipment Lists
- Spares Management Strategy
Operations & Maintenance Training
Operation and maintenance training gives clients a thorough understanding of their plant equipment and the systems they operate in. Trained staff with the requisite skills will improve safety and standardized work practices, while reducing the plant maintenance costs over the lifetime of the equipment.
Final Documentation
The end of project report is used by project managers and their team to determine how the project performed summarising in :
- Document what the project team delivered
- Provide a project evaluation in terms of work quality
- Evaluate budget and schedule performance
Project Closeout
The Project closeout works includes signing off successful completion and handover letters / waranties, collection of final payments and project team winding of their site project office apart from signing off regulatory agreements.
Meeting International Standards
The Group has been working with reputed manufacturers and service providers in diverse geographic locations for over two decades conforming to international standards like :
⎮DIN
⎮ ASA
⎮ ANSI
⎮ ASME
⎮ IEEE
⎮ ISO
⎮
⎮
BS ⎮ AESC
⎮
BIS
⎮
CE
⎮
FIDIC ⎮
Interested in our services? We’re here to help!
We want to know your needs exactly so that we can provide the perfect solution. Let us know what you want and we’ll do our best to help.